What's the Secret to Automated Water Bottle Production? 10 Steps Revealed
10/11/20235 min read
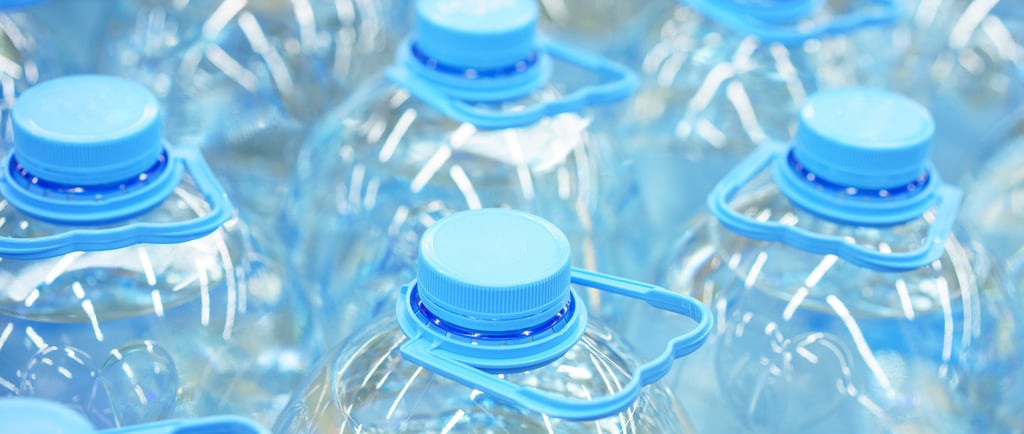
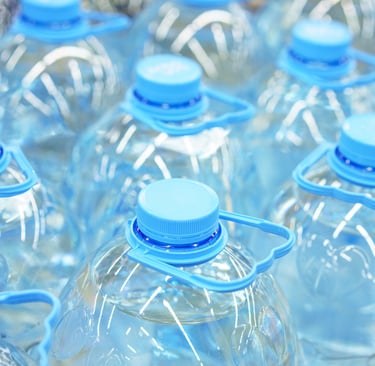
In the world of manufacturing, automation is the key to efficiency, consistency, and costeffectiveness. One industry that has greatly benefited from automated processes is the production of water bottles. From the initial sourcing of water to the final sealing of the bottle, automation has revolutionized the way water bottles are manufactured. In this article, we will unveil the 10 steps involved in automated water bottle production, shedding light on the secrets behind this fascinating process.
Step 1: Water Sourcing and Treatment
The journey of a water bottle begins with the sourcing of water. Whether it's spring water, purified water, or mineral water, the source must meet quality standards. Automated systems are used to extract water from its source and then treat it to remove impurities and ensure it meets regulatory requirements.
Example: Spring Water Sourcing
Imagine a picturesque spring nestled in the mountains. Automated pumps draw water from the spring and pass it through a series of filters to remove sediment and impurities. The water is then treated with ozone or ultraviolet (UV) light to disinfect it, ensuring it's safe for consumption.
Step 2: Bottle Manufacturing
Automated machines are used to manufacture the bottles themselves. This process involves the extrusion of plastic materials, such as PET (Polyethylene Terephthalate), into preforms. These preforms are then heated and blown into the shape of the final bottle using blow molding machines.
Example: Blow Molding
In a high-tech manufacturing facility, rows of blow molding machines work in perfect harmony. Preforms are loaded into the machines, heated until they soften, and then rapidly inflated into bottle shapes using compressed air. This automated process ensures uniform bottle quality and shape.
Step 3: Label Printing
Labels play a crucial role in branding and providing essential information to consumers. Automated label printing machines apply labels to the bottles with precision and consistency. These labels can be customized to include branding, nutritional information, and more.
Example: Customized Labeling
In a label printing facility, digital printers seamlessly apply labels to water bottles. These labels can be tailored to suit various bottle sizes and shapes, incorporating vibrant graphics and essential details. Automation ensures that each label adheres perfectly to every bottle, enhancing brand consistency.
Step 4: Filling
Filling the bottles with water is a critical step in the production process. Automated filling machines ensure that each bottle is filled to the correct level, minimizing wastage and ensuring product consistency.
Example: Precision Filling
Imagine a conveyor belt carrying rows of empty bottles. As they pass through the filling station, automated nozzles dispense the precise amount of water into each bottle. Sensors monitor the fill levels to guarantee accuracy and prevent overfilling or underfilling.
Step 5: Capping
Capping machines are used to securely seal the bottles. Various types of caps, such as screw caps, sports caps, and tamper-evident caps, can be applied depending on the product and packaging requirements.
Example: Tamper-Evident Sealing
Tamper-evident caps are equipped with a plastic ring that breaks when the cap is twisted open, indicating that the bottle has been tampered with. Automated capping machines precisely apply these caps, ensuring that each bottle remains sealed until it reaches the consumer.
Step 6: Inspection
Automated inspection systems use cameras and sensors to check for defects in the bottles, labels, and caps. Any faulty items are automatically removed from the production line to maintain product quality.
Example: Vision Inspection High-speed cameras capture images of each passing bottle, while specialized software analyzes these images for defects. If a bottle with a misaligned label or a cap defect is detected, robotic arms swiftly divert it from the production line, ensuring only flawless products proceed.
Step 7: Quality Control
Quality control processes include conducting tests to ensure the water meets safety and purity standards. Automated systems sample and analyze water from each batch to ensure compliance with regulatory requirements.
Example: Water Purity Testing
In a state-of-the-art laboratory, automated sampling devices collect water samples from production batches. These samples undergo rigorous testing for contaminants, pH levels, and other quality parameters. Any deviation from standards triggers immediate corrective actions.
Step 8: Packaging
Once the bottles have been filled, capped, and inspected, they are ready for packaging. Automated packaging machines can place bottles in boxes, shrink-wrap them, or pack them in other suitable containers for distribution.
The packaging stage in automated water bottle production involves several processes to ensure that the bottles are properly prepared for distribution. These processes include:
1. Packaging: Bottles are placed into cartons or boxes. Automated machinery is used to efficiently load the bottles into the designated packaging, which could be cardboard cartons, plastic containers, or other suitable packaging materials.
Example: Carton Loading
In the packaging facility, automated robots or machines carefully place bottles into cartons. These cartons are designed to hold a specific quantity of bottles, ensuring efficient and uniform packaging.
2. Sealing: Once the bottles are placed inside the cartons, automated equipment is employed to seal the cartons securely. Typically, this is done using adhesive tape or another sealing method to prevent tampering and ensure the integrity of the packaging.
Example: Automated Carton Sealing
Automated carton sealing machines apply adhesive tape to seal the cartons. This ensures that the bottles remain securely enclosed and protected until they reach their destination.
3. Palletizing: For high-volume transport and efficient handling, cartons of packaged bottles are arranged on pallets. Automated palletizing machines are used to stack the cartons on pallets in a stable and organized manner, ready for transportation. Example: Palletization for Transport In the palletizing area, automated systems stack cartons of water bottles onto pallets. These machines optimize the arrangement to maximize the number of cartons on each pallet while ensuring stability and ease of handling.
Example: Palletization for Transport
In the palletizing area, automated systems stack cartons of water bottles onto pallets. These machines optimize the arrangement to maximize the number of cartons on each pallet while ensuring stability and ease of handling.
The combination of these sub-processes ensures that the water bottles are securely packaged, sealed, and palletized for efficient and safe transportation to their intended destinations. Automation in this step minimizes the risk of errors, reduces manual labor, and enhances the overall efficiency of the packaging process.
Step 9: Transportation
Automated conveyor systems transport the finished water bottles from one production stage to the next, minimizing manual handling and streamlining the entire process.
Example: Conveyor Belt Efficiency
Conveyor belts crisscross the manufacturing facility, seamlessly transporting bottles from one station to another. This automation not only reduces the risk of damage but also ensures a continuous and efficient flow of bottles throughout the production line.
Step 10: Distribution
The final step in automated water bottle production is distribution. Automated systems track inventory levels and manage the shipping process, ensuring that products reach their intended destinations efficiently and on time.
Example: Inventory Management
In a distribution center, automated inventory management systems track the stock of bottled water in real-time. When the inventory falls below a certain threshold, the system automatically generates orders for replenishment, ensuring that retailers and consumers receive their products promptly.
In conclusion, automation has completely transformed the manufacturing process of water bottles. From sourcing and treatment to distribution, each step benefits from automation's precision, efficiency, and consistency. Manufacturers in the water bottle industry have harnessed the power of automation to deliver high-quality products to consumers worldwide. As technology continues to advance, we can expect even more innovations in automated manufacturing, further improving the efficiency and sustainability of this essential industry.
If you want to find out more about how automation can revolutionize your water bottle production, don't hesitate to contact us for a free consultation. We're here to help you unlock the secrets to success in automated manufacturing. You can reach us at +60 19 268 9812 (Mr. Rajaa)
© 2024 T-Robot. All Rights Reserved.