What's the Secret Behind Perfect Packaging? Manual or Automated?
10/3/20234 min read
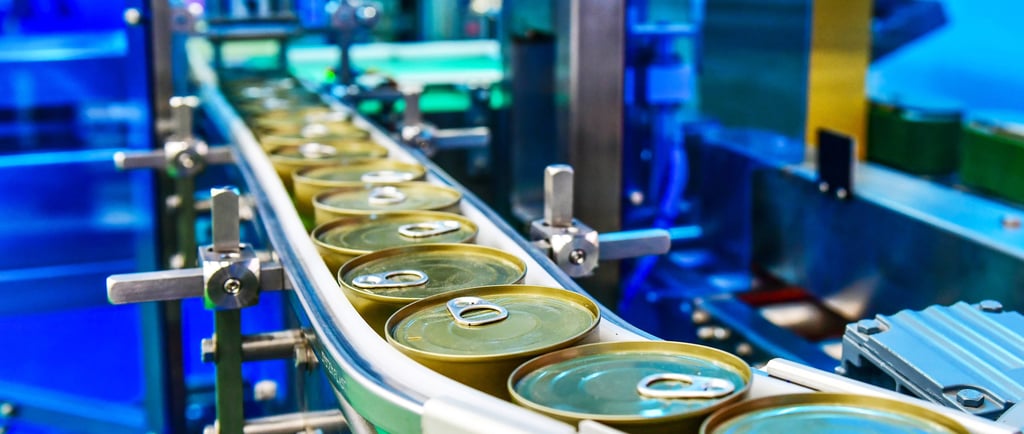
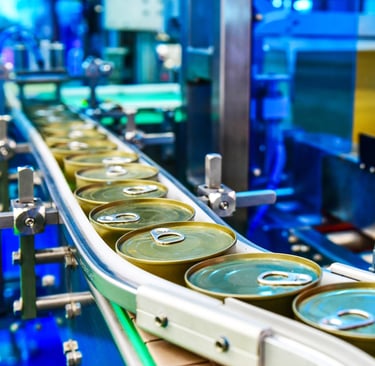
If you've ever wondered how products make their way from factories to store shelves, packaging plays a crucial role in this journey. Packaging is the final step in preparing products for distribution, and it can be a complex process, especially when dealing with high-volume products. In this article, we will explore the world of packaging, focusing on the differences between manual and automated packaging systems. We'll use the food industry as an example and delve into various packaging methods, such as plastic and cartons, to illustrate how automation is changing the game.
Introduction to Packaging
Packaging is the art and science of enclosing products in protective materials to ensure they reach consumers in optimal condition. It serves several essential purposes:
1. Protection: Packaging safeguards products from external factors like moisture, dust, and physical damage during transportation and storage.
2. Identification: Packaging often includes labeling and branding, making it easier for consumers to identify and choose products.
3. Information: It provides essential information about the product, such as ingredients, nutritional facts, and usage instructions.
4. Convenience: Packaging can make products easy to handle, carry, and store.
5. Marketing: It plays a crucial role in marketing by attracting consumers' attention and conveying a brand's message.
Manual Packaging Systems Manual packaging systems involve human labor in every step of the packaging process. Here's how it typically works:
1. Product Preparation: Workers gather the products to be packaged and arrange them for packaging.
2. Filling and Sealing: Products are manually placed into containers or packages, and lids or seals are applied by hand.
3. Quality Control: Workers inspect packages for defects, ensuring they meet quality standards.
4. Labeling and Printing: Labels and print information are applied to packages manually.
5. Palletization: Finished packages are stacked on pallets, ready for distribution.
Manual packaging has its advantages, such as flexibility and lower upfront costs. Small businesses or those dealing with limited production runs may find manual packaging more suitable. However, it has several drawbacks:
- Slower Production: Manual processes are slower, limiting the production capacity.
- Labor Costs: High labor costs are associated with manual packaging, especially for large volumes.
- Inconsistency: Human error can lead to inconsistencies in packaging quality.
Automated Packaging Systems
Automated packaging systems, on the other hand, use machinery and technology to perform packaging tasks. Here's how they work:
1. Product Feeding: Products are fed into the packaging machine through a conveyor belt or other automated mechanisms.
2. Filling and Sealing: Machines measure, fill, and seal packages with precision.
3. Quality Control: Automated sensors and cameras inspect packages for defects, ensuring consistent quality.
4. Labeling and Printing: Labels and print information are applied automatically.
5. Palletization: Robotic arms or machines stack packages on pallets, ready for distribution.
Automated packaging systems offer several advantages:
- Increased Efficiency: Automated systems work faster, leading to higher production rates.
- Reduced Labor Costs: Fewer workers are required, leading to cost savings.
- Consistency: Automation reduces the risk of errors and ensures consistent product quality.
- Data Collection: Automated systems can collect data on packaging processes for quality control and analysis.
A Real-Life Example: The Food Industry
Let's dive deeper into the packaging processes of the food industry, a sector that heavily relies on both manual and automated packaging systems. We'll explore how automation has revolutionized packaging in this field.
a) Packaging in Plastic
Manual Packaging
In a manual plastic packaging process, workers are responsible for placing food items in plastic containers or bags. This process is slow and labor-intensive. Workers must ensure that the containers are sealed tightly to prevent contamination and preserve freshness.
Automated Packaging
Automated packaging systems for plastic containers use machines that can fill, seal, and label thousands of containers per hour. These machines are equipped with sensors to detect any defects or irregularities in the packaging, ensuring a consistently high-quality end product.
b) Packaging in Cartons
Manual Packaging
In the manual carton packaging process, workers fold and assemble cardboard cartons, place products inside, and then seal them. This process is time-consuming and relies heavily on the precision of the workers. Automated Packaging Automated carton packaging systems use machines that can rapidly fold and assemble cartons, place products inside, and seal them with adhesive or tape. These machines can handle various carton sizes and shapes, making them highly adaptable to different product lines.
Automated Packaging
Automated carton packaging systems use machines that can rapidly fold and assemble cartons, place products inside, and seal them with adhesive or tape. These machines can handle various carton sizes and shapes, making them highly adaptable to different product lines.
Comparing Manual and Automated Packaging
Now that we've looked at packaging in plastic and cartons let's compare manual and automated systems in the food industry:
Speed
- Manual: Slow and limited by the pace of human workers.
- Automated: Much faster, capable of handling high volumes efficiently.
Labor Costs
- Manual: High labor costs due to the need for many workers.
- Automated: Lower labor costs, with fewer workers needed for supervision.
Consistency
- Manual: Prone to human error, leading to inconsistencies in packaging quality.
- Automated: Consistently high-quality packaging with minimal errors.
Adaptability
- Manual: Less adaptable to changes in product types or packaging designs.
- Automated: Highly adaptable, with settings that can be easily adjusted for different products.
Quality Control
- Manual: Limited quality control, relying on visual inspection by workers.
- Automated: Robust quality control through sensors and cameras, ensuring consistent quality
Packaging is a critical aspect of getting products from manufacturers to consumers, and the choice between manual and automated packaging systems can have a significant impact on efficiency, cost, and quality. While manual packaging systems offer flexibility and can be suitable for smaller businesses or specialized products, automated systems excel in high-volume environments, delivering faster production, lower labor costs, and consistent quality.
In our example from the food industry, we've seen how automation has transformed packaging processes, making them faster, more reliable, and adaptable to various product types and packaging formats. As technology continues to advance, automated packaging systems will likely become even more sophisticated, further improving efficiency and reducing costs.
Whether it's plastic containers, cardboard cartons, or other packaging materials, the choice between manual and automated systems should be based on the specific needs of a business, considering factors like production volume, labor availability, and quality requirements. Ultimately, the goal of packaging systems is to ensure that products reach consumers in the best possible condition, and the right choice of packaging technology plays a crucial role in achieving that goal.
Contact Us for Free Consultation
Ready to take your business to the next level with automated machines and systems? Contact us today at +60 19 268 9812 (Mr. Rajaa) for a free consultation. Our experts will help you explore the best solutions tailored to your specific needs, ensuring a seamless integration of cutting-edge technologies into your production processes.
© 2024 T-Robot. All Rights Reserved.