Vision Systems Revealed! Uncovering the Secrets of Industrial Camera Mechanics
8/10/20233 min read
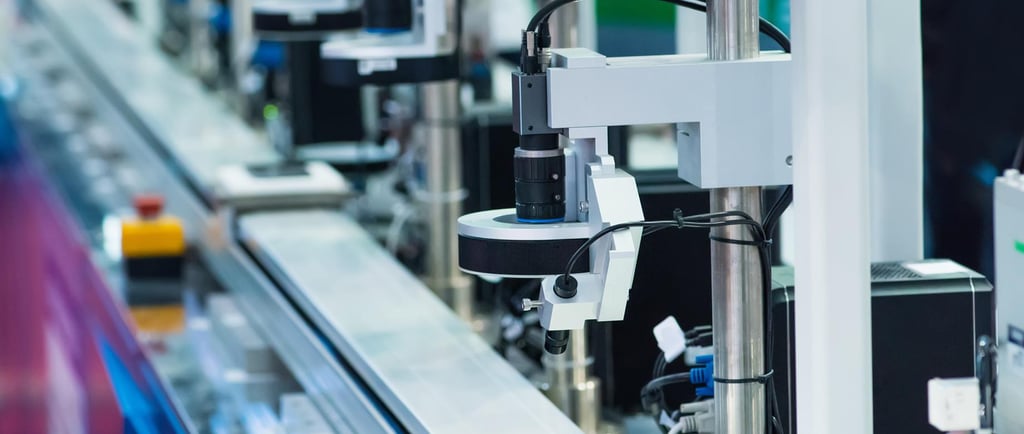

In today's rapidly advancing technological landscape, the term "automation" has become synonymous with increased efficiency, accuracy, and productivity. One of the key players driving this transformation is the integration of vision systems powered by industrial cameras. These cuttingedge devices, often unseen but ever-present, are the eyes of modern automation, enabling machines to perceive and interpret their surroundings. If you've ever wondered how industrial cameras work within automation processes and their diverse applications, this article is your gateway to understanding the fascinating world of vision systems.
The Role of Industrial Cameras in Automation
Imagine a scenario where a manufacturing plant needs to inspect thousands of tiny components for defects or verify the correct labeling on products before they're packaged and shipped. In such scenarios, human inspection would be time-consuming, prone to errors, and not feasible on a large scale. This is where industrial cameras step in as crucial tools for automation.
You might be wondering, "How exactly do these cameras work and make automation so efficient?" Well, let's dive into the inner workings of industrial cameras and how they play a pivotal role in various automated processes.
How Do Industrial Cameras Work?
At its core, an industrial camera is a highly specialized imaging device designed to capture visual data from the environment. These cameras are equipped with advanced optics, sensors, and interfaces that allow them to acquire images or videos of the objects they're pointed at. The real magic, however, lies in the processing and interpretation of these images.
You might be surprised to know that industrial cameras don't just passively capture images. They're often part of larger vision systems that include powerful computers and specialized software. Here's a breakdown of how industrial cameras work in automation:
1. Image Capture: The camera lens focuses light onto a sensor, typically a Charge-Coupled Device (CCD) or a Complementary Metal-Oxide-Semiconductor (CMOS) sensor. These sensors convert light into electrical signals, creating a digital representation of the visual scene.
2. Signal Processing: The electrical signals generated by the sensor are then processed by the camera's onboard processing unit. This step involves amplifying, digitizing, and correcting the signals to produce a high-quality image.
3. Data Transmission: Once processed, the digital image data is sent via high-speed interfaces (such as USB, GigE, or Camera Link) to a connected computer or controller.
4. Image Analysis: This is where the real magic happens. The captured images are analyzed by specialized software algorithms. These algorithms can detect patterns, shapes, colors, textures, and even minute defects. The data extracted from the images is used to make informed decisions and trigger actions based on predefined criteria.
5. Decision Making and Automation: The analyzed data is interpreted by the system's software. For instance, in a manufacturing line, the software can decide whether a product is defective or if it meets specific quality standards. These decisions can then trigger automated processes, such as sorting, rejecting, or alerting human operators.
Applications of Industrial Cameras in Automation
The applications of industrial cameras in automation are vast and diverse. They span across industries and have revolutionized manufacturing, quality control, and various other processes. Here are a few notable examples:
1. Quality Control: Industrial cameras play a critical role in inspecting products for defects, ensuring consistency in size, shape, color, and overall quality. They can identify imperfections that are often imperceptible to the human eye.
2. Robot Guidance: Vision systems enable robots to "see" their surroundings, helping them navigate, pick and place objects accurately, and perform complex tasks with precision.
3. Barcode and OCR Reading: Cameras equipped with Optical Character Recognition (OCR) capabilities can read text and barcodes on products, facilitating inventory tracking, product identification, and automated data entry.
4. Medical Imaging: In healthcare, industrial cameras contribute to medical imaging systems, aiding in diagnostics, surgeries, and research.
5. Agriculture: Vision systems can be used in automated agriculture processes, such as identifying and sorting ripe fruits, inspecting crops for diseases, and optimizing irrigation.
6. Logistics and Warehousing: Cameras are used for package sorting, inventory management, and tracking goods in large warehouses, streamlining supply chain operations.
In conclusion, Industrial cameras are the unassuming heroes of automation, providing machines with the ability to "see" and interpret the world around them. From quality control to robotic guidance, these devices have revolutionized various industries by increasing efficiency, accuracy, and productivity. As you delve into the world of automation, understanding the inner workings of vision systems and their applications will give you a deeper appreciation for the technology that drives modern industrial processes.
Contact Us for Free Consultation
Ready to take your business to the next level with automated machines and systems? Contact us today at +60 19 268 9812 (Mr. Rajaa) for a free consultation. Our experts will help you explore the best solutions tailored to your specific needs, ensuring a seamless integration of cutting-edge technologies into your production processes.
© 2024 T-Robot. All Rights Reserved.