Streamlining Sorting: How Automation Transforms High-Volume Product Management
9/22/20234 min read
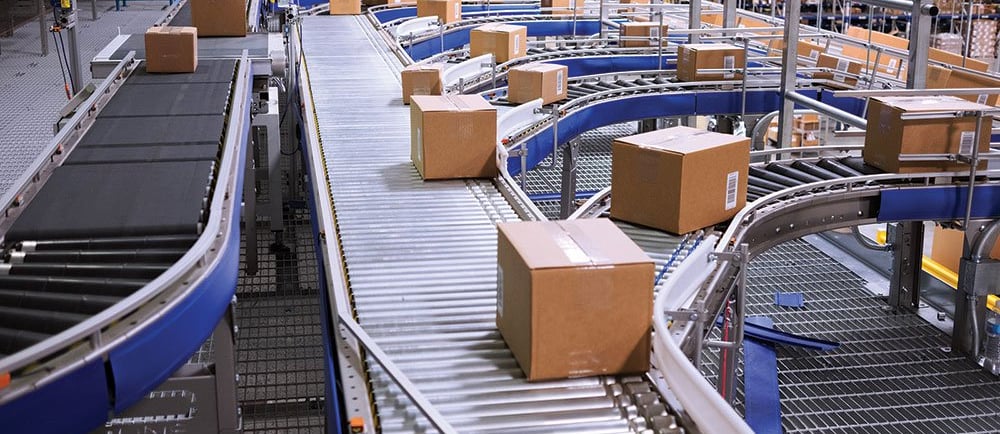
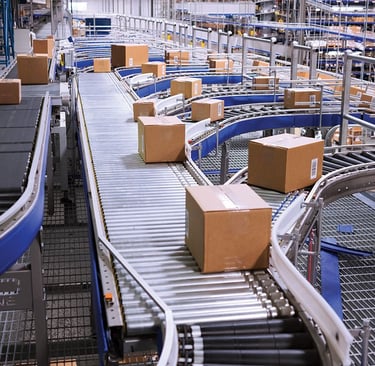
If you've ever wondered how products swiftly find their way into the right packages, onto the right shelves, or down the right assembly line, you're about to discover the magic behind it. Sorting systems are the unsung heroes of many industries, ensuring that items are organized efficiently. In this article, we'll delve into the world of sorting systems, focusing on high-volume product management and the game-changing impact of automation. We'll use the example of the manufacturing industry to illustrate these concepts, and we'll explore various automated sorting methods, including vibration bowls, conveyors with barricades, blockers, and indexing systems.
The Sorting Challenge
Imagine a bustling factory where thousands of components, ranging from tiny screws to large metal plates, need to be organized and sent to various production lines. The traditional method of sorting involves human labor. Workers manually sift through the items, segregating them based on size, weight, or other criteria. This process, while effective to some extent, comes with several drawbacks.
Manual Sorting System
1. Slower Pace
Manual sorting is labor-intensive, which means it can only move as fast as human workers. Even with the most diligent employees, the pace of sorting is limited, and it often falls behind the speed of modern production lines.
2. Human Error
As dedicated as workers may be, they are prone to making mistakes. Fatigue, distractions, and variations in judgment can lead to incorrect sorting, causing bottlenecks, delays, and quality issues.
3. Labor Costs
Hiring and maintaining a skilled workforce for sorting tasks can be expensive, especially in regions with high labor costs. Moreover, manual labor comes with additional expenses like benefits and training.
4. Monotony
Performing repetitive sorting tasks can be monotonous and lead to worker dissatisfaction, high turnover rates, and the risk of accidents due to fatigue.
Enter Automation: A Game Changer
To overcome the limitations of manual sorting, many industries have turned to automation. Automation in sorting systems involves using machines, sensors, and software to streamline the process. Here's how automation addresses the challenges posed by manual sorting:
Automated Sorting System
1. Speed and Efficiency
Automated sorting systems are significantly faster than their manual counterparts. Machines can process items at a constant, high-speed rate, ensuring that production lines keep up with demand.
2. Accuracy and Consistency
Machines are programmed to be highly precise and consistent. They don't get tired, distracted, or make errors due to judgment. This translates to higher accuracy in sorting, reducing the chances of mistakes.
3. Cost-Effectiveness
While initial setup costs for automated systems can be substantial, they often result in longterm savings. Fewer labor requirements, reduced error rates, and increased efficiency can lead to significant cost reductions over time.
4. Improved Working Conditions
Automation frees workers from repetitive and physically demanding sorting tasks, allowing them to focus on more complex and fulfilling roles within the production process. This can lead to improved job satisfaction and reduced turnover.
Automation in Action: Manufacturing Industry
Let's explore how automation revolutionizes high-volume product management in the manufacturing industry through a few practical examples.
1. Vibration Bowl Sorters
Vibration bowl sorters are a common sight in manufacturing facilities. They consist of a bowl shaped chamber with a spiral track running along its inner surface. Products are poured into the bowl, and the vibrations generated by the machine cause the items to move along the spiral track.
How It Works:
1. Products are poured into the bowl.
2. The machine generates controlled vibrations that move the items along the spiral track.
3. As the items move, they are oriented and sorted based on their size or other criteria.
4. The sorted items exit the bowl one by one, ready for further processing or packaging.
Advantages:
High-speed sorting.
Accurate and consistent sorting.
Suitable for small to medium-sized items.
Reduces the need for manual labor.
2. Conveyors with Barricades
Conveyors are essential for transporting items within a facility, and they can be enhanced with automated sorting capabilities. Conveyors equipped with barricades use physical barriers to divert items onto different paths.
How It Works:
1. Products are placed on a conveyor belt.
2. Automated barricades are strategically positioned along the conveyor's path.
3. Sensors detect the characteristics of the items and determine their destination.
4. The barricades activate to divert items onto the appropriate path for sorting.
Advantages:
Continuous and automated sorting.
Suitable for a wide range of product sizes and shapes.
Versatile sorting options based on sensor inputs.
Integration with existing conveyor systems.
Application:
Conveyors with barricades are commonly used in the automotive industry to sort various components like bolts, nuts, and small parts.
3. Blockers and Indexing Systems
Blockers and indexing systems are used to control the flow of items along a conveyor line. They create temporary stops or pauses in the production process, allowing for precise sorting or assembly.
How It Works:
1. Items move along a conveyor line.
2. Blockers are activated to stop or divert specific items.
3. Indexing systems control the spacing and alignment of items for precise sorting or assembly.
4. Once sorted or assembled, items continue down the conveyor line.
Advantages:
Precise control over item placement and sorting.
Ensures proper alignment for assembly processes.
Ideal for sorting items with complex shapes or assembly requirements.
Enhances overall production quality and efficiency.
Application:
Blockers and indexing systems are commonly used in the food and beverage industry for packaging and quality control, such as aligning bottles before capping or filling.
In conclusion, Automation has brought about a paradigm shift in high-volume product management, especially in industries like manufacturing. It offers speed, accuracy, cost-effectiveness, and improved working conditions compared to manual sorting systems. Through examples like vibration bowl sorters, conveyors with barricades, blockers, and indexing systems, we've seen how automation can streamline sorting processes and enhance overall production efficiency.
As industries continue to evolve and embrace automation, it's clear that the future of high-volume product management lies in the hands of machines. However, it's essential to remember that automation is not a one-size-fits-all solution. The choice of sorting system depends on the specific needs and characteristics of the products being handled. With automation paving the way for more efficient sorting, businesses can expect improved productivity, reduced errors, and a competitive edge in the fast-paced world of modern manufacturing.
Contact Us for Free Consultation
Ready to take your business to the next level with automated machines and systems? Contact us today at +60 19 268 9812 (Mr. Rajaa) for a free consultation. Our experts will help you explore the best solutions tailored to your specific needs, ensuring a seamless integration of cutting-edge technologies into your production processes.
© 2024 T-Robot. All Rights Reserved.