Speed It Up! 4 Aspects That Set Industrial Robot Pace!
8/28/20236 min read
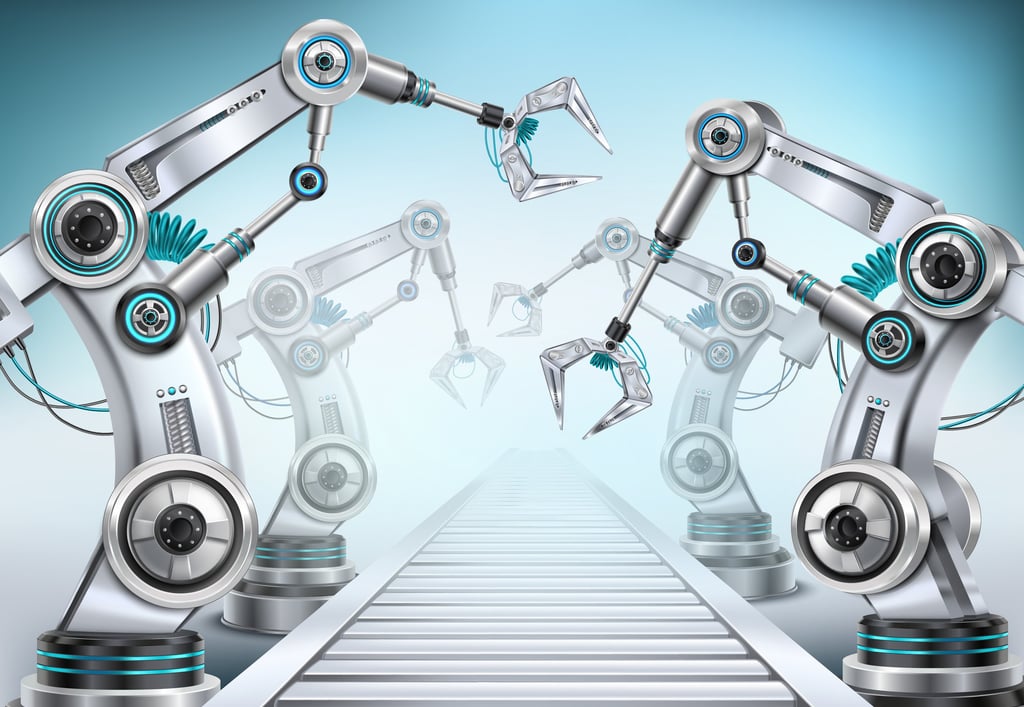
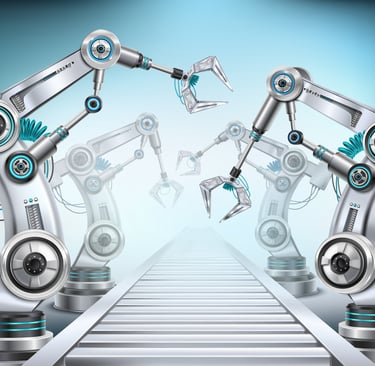
Industrial robots have become a cornerstone of modern manufacturing, revolutionizing the way products are assembled, packaged, and moved within production facilities. These robots have a wide range of applications, each requiring a specific set of capabilities and performance parameters. One of the critical factors in determining the effectiveness of an industrial robot is its speed. The speed at which an industrial robot operates is a complex interplay of factors, including the type of application, the size and weight of the products being handled, and the need for precision and consistency. In this article, we will explore the different factors that influence the speed of industrial robots and how they are optimized for various applications.
The Versatility of Industrial Robots
Industrial robots are incredibly versatile machines that can be programmed to perform a wide range of tasks in various industries. Some common applications include welding, painting, assembly, material handling, and packaging. Each of these applications has its unique requirements, including the necessary speed of operation.
Speed in Industrial Robots: It's More Than Just a Number
When discussing the speed of industrial robots, it's essential to recognize that it's more than just a single metric. The speed of a robot is influenced by various factors, and depending on the specific task, different aspects of speed become critical. These factors can be broadly categorized into three main areas:
1. Linear Speed: This refers to how fast the robot can move from one point to another in a straight line. It is essential for tasks that involve transporting products within a manufacturing facility or moving from one assembly station to another. Linear speed is typically measured in meters per second (m/s) or millimeters per second (mm/s).
2. Rotational Speed: For tasks that require rotating components or manipulating objects, such as welding or painting, rotational speed is a crucial factor. This is typically measured in degrees per second (°/s) or revolutions per minute (RPM).
3. Cycle Time: The cycle time of an industrial robot is the total time it takes to complete a single operation, from start to finish. This includes not only the time spent on the actual task but also factors like loading and unloading. Cycle time is vital for determining the overall production output of a robot.
Factors Influencing Robot Speed
The speed at which an industrial robot can operate is influenced by a multitude of factors, including:
1. Payload Capacity
The payload capacity of a robot refers to the maximum weight it can carry while performing its task. Larger robots with higher payload capacities tend to move more slowly because they need to maintain stability and avoid undue wear and tear on their components. Smaller robots, on the other hand, can move faster when handling lighter objects.
2. Inertia
Inertia is the resistance of an object to changes in its motion. When an industrial robot is tasked with moving an object, its speed must be controlled to account for the inertia of the object. This is especially important when dealing with heavy or bulky items, as abrupt movements can lead to instability and imprecise positioning.
3. Accuracy and Precision
Some applications demand a high degree of accuracy and precision, such as when assembling intricate electronic components or performing delicate surgical procedures. In such cases, the robot may need to move more slowly to ensure that every movement is controlled and precise.
4. Safety
Safety is a paramount concern in industrial settings. Robots must be programmed to operate at speeds that are safe for both the equipment and the workers. Safety features such as collision detection and emergency stop systems are essential components of industrial robot speed control.
5. End-Effector Design
The end-effector, or the tool attached to the robot's arm, also plays a crucial role in determining speed. Different end-effectors are designed for specific tasks, and their design can influence how fast the robot can perform those tasks. For example, a robot equipped with a high-speed gripper may be able to pick and place items rapidly, while a robot with a welding torch may have a slower but more controlled pace.
6. Programming
The speed of an industrial robot is ultimately determined by its programming. Robot programmers can adjust the speed of individual movements, acceleration, and deceleration rates to optimize the robot's performance for a specific task. The skill and expertise of the programmer are essential in achieving the desired speed and precision.
Applications and Speed Requirements
Let's delve into some specific industrial robot applications to understand how speed requirements differ based on the task:
1. Material Handling
In material handling applications, robots are responsible for transporting raw materials or finished products within a facility. The speed at which these robots operate is often a balance between efficiency and safety. They need to move quickly to maintain a high production output, but not so fast that it compromises the safety of nearby workers or the integrity of the products being transported.
2. Welding
In welding applications, precision and control are paramount. Robots used for welding must move at a pace that allows them to deposit welds accurately. The speed depends on factors such as the type of welding being performed (arc welding, spot welding, etc.) and the material thickness.
3. Painting
Painting robots need to move at a consistent speed to ensure an even and uniform coat of paint. Speed control is essential in preventing drips or uneven coverage. These robots are also equipped with precise control systems to manage paint flow and spray patterns.
4. Assembly
In assembly tasks, robots may need to work at different speeds for different components. Some components may require a slower, more precise approach, while others can be assembled at a faster pace. The overall speed of the assembly process is optimized to meet production targets while maintaining quality.
5. Packaging
Robots used in packaging applications often operate at high speeds, especially when handling small and lightweight products. However, they must also be programmed to ensure that the packaging process is consistent and accurate. Any variations in speed or positioning can lead to packaging errors.
6. Surgical Robots
In the field of medicine, surgical robots are used for minimally invasive procedures. These robots need to move slowly and precisely to perform delicate surgeries with the utmost care and accuracy. Speed in this context is secondary to precision and safety.
The Future of Industrial Robot Speed
As technology advances, so does the potential for faster and more efficient industrial robots. Here are some trends and developments that are shaping the future of robot speed:
1. Advanced Programming and Control Systems
The continued development of advanced programming languages and control systems allows for finer control over robot movements. This will enable robots to operate at optimal speeds for a wider range of tasks, improving efficiency and productivity.
2. Sensor Technology
The integration of advanced sensors, such as vision systems and force sensors, allows robots to adapt their speed and movements in real-time based on the environment and the objects they are interacting with. This enhances both safety and performance.
3. Collaborative Robots (Cobots)
Collaborative robots, or cobots, are designed to work alongside humans. They are often programmed to operate at lower speeds and with built-in safety features to prevent collisions with human workers. The development of cobots is expanding the range of tasks that robots can perform in various industries.
4. Machine Learning and Artificial Intelligence
Machine learning and artificial intelligence are being used to optimize robot performance. These technologies can analyze data from sensors and make real-time adjustments to robot movements, allowing for more efficient and adaptive speed control.
5. Energy Efficiency
Efforts are being made to design robots that operate more energy-efficiently, which can have a positive impact on speed. Energy-efficient robots can move faster for longer periods without overheating or requiring frequent downtime for recharging.
In conclusion, The speed at which an industrial robot can operate is a critical factor that impacts its effectiveness in various applications. Different factors, including payload capacity, inertia, accuracy, safety, end-effector design, and programming, influence the speed of these robots. Depending on the application, robots may need to move slowly for precision tasks or operate at high speeds for efficient material handling and packaging.
As technology continues to advance, industrial robots are becoming more versatile and capable of operating at optimal speeds for a wide range of tasks. Advanced programming, sensor technology, collaborative robots, machine learning, and energy efficiency are all contributing to the evolution of industrial robot speed.
In the future, we can expect industrial robots to become even faster, more precise, and adaptable, further revolutionizing the manufacturing industry and expanding their role in various other sectors, including healthcare, logistics, and beyond.
Contact Us for Free Consultation
Ready to take your business to the next level with automated machines and systems? Contact us today at +60 19 268 9812 (Mr. Rajaa) for a free consultation. Our experts will help you explore the best solutions tailored to your specific needs, ensuring a seamless integration of cutting-edge technologies into your production processes.
© 2024 T-Robot. All Rights Reserved.