Is Manual or Automated Quality Control the Key to High-Volume Product Success?
9/12/20234 min read
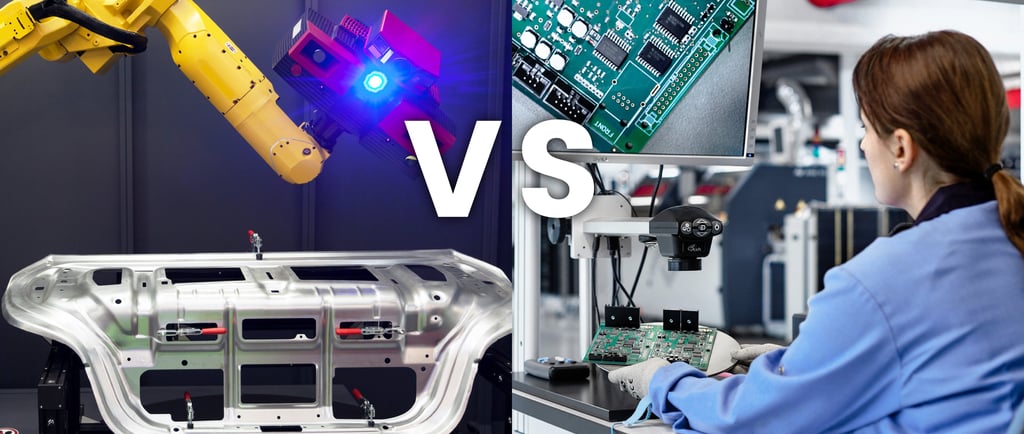
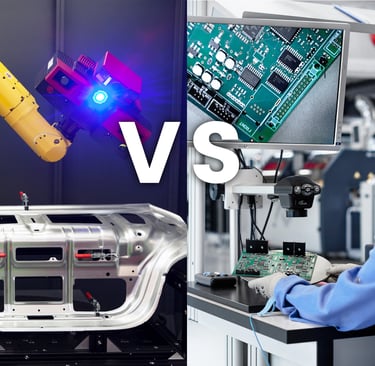
In today's fast-paced world, managing high-volume products efficiently is crucial for businesses in various industries. From manufacturing to e-commerce, companies often deal with large quantities of products that need to meet quality standards before reaching the hands of consumers. In this article, we'll explore how to manage high-volume products, with a focus on quality control (QC) systems. We'll compare manual QC systems to automated ones, and illustrate the concepts with an example from the automotive industry.
High-Volume Production
High-volume products are those that are produced in large quantities, typically due to high demand or cost-effective manufacturing processes. Examples include smartphones, clothing, food items, and automobiles. Ensuring the quality of these products is essential to maintain customer satisfaction, uphold brand reputation, and comply with industry regulations. Quality control is the process through which businesses assess and maintain product quality, and it can be done manually or automatically.
Manual Quality Control
Manual quality control involves human intervention at various stages of the production process to inspect and assess product quality. This process typically includes visual inspections, tactile examinations, and measurements using tools and instruments. Let's delve into the key aspects of manual QC:
1. Visual Inspections
Visual inspections are a fundamental aspect of manual QC. Skilled inspectors examine products for defects, irregularities, and deviations from quality standards. This process relies on the human eye to identify issues such as scratches, dents, or misalignments.
2. Tactile Examinations
In addition to visual inspections, manual QC may involve tactile examinations. This includes touching and feeling the product to identify defects that may not be visible to the naked eye. For example, a clothing manufacturer might feel the fabric for roughness or loose threads.
3. Measurement Tools
Measurement tools like calipers, micrometers, and gauges are used to precisely measure product dimensions. This is critical in industries where even small variations can affect product functionality or safety.
Pros of Manual QC
1. Flexibility: Manual QC allows for quick adjustments and adaptations to changing product requirements or unexpected issues.
2. Skill and Expertise: Skilled inspectors can detect subtle defects that automated systems might miss.
3. Cost-Effective for Small Batches: In situations where production volumes are relatively low, manual QC can be cost-effective.
Cons of Manual QC
1. Inconsistency: Human error and fatigue can lead to inconsistent results, affecting product quality.
2. Limited Scalability: Manual QC becomes impractical and costly for large-scale production.
3. Time-Consuming: Manual inspections can slow down the production process.
Automated Quality Control
Automated quality control relies on machinery, sensors, cameras, and software to inspect and assess product quality. These systems are designed to perform repetitive tasks with precision and speed. Here's a closer look at automated QC:
1. Sensors and Cameras
Automated QC systems use sensors and cameras to capture data and images of products. These sensors can detect defects, measure dimensions, and even identify variations in color or texture.
2. Machine Learning and AI
Many automated QC systems incorporate machine learning and artificial intelligence (AI) algorithms. These algorithms can analyze data and images to detect defects or anomalies that may not be apparent to the human eye.
3. Robotics
In some industries, robots are used for QC purposes. They can perform tasks such as assembly, welding, or picking and placing items with high precision.
Pros of Automated QC
1. Consistency: Automated systems provide consistent and reliable results, reducing the risk of human error.
2. High Speed: Automated QC is much faster than manual inspection, making it suitable for highvolume production.
3. 24/7 Operation: Automated systems can operate continuously, ensuring quality control around the clock.
Cons of Automated QC
1. Initial Investment: Setting up automated QC systems can be expensive, especially for smaller businesses.
2. Complexity: Maintaining and fine-tuning automated systems may require specialized expertise.
3. Limited Adaptability: Automated systems may struggle to adapt to unexpected changes or new product designs.
A Case Study: Automotive Industry
To illustrate the concepts of manual and automated QC, let's consider the automotive industry, which produces high-volume products with stringent quality requirements.
Manual QC in the Automotive Industry
In traditional automotive manufacturing, manual QC plays a significant role. Skilled inspectors visually examine vehicles at various stages of assembly, checking for paint defects, panel alignments, and interior finish quality. They also conduct road tests to evaluate performance and functionality.
Automated QC in the Automotive Industry
In recent years, the automotive industry has increasingly embraced automated QC technologies. Here are some examples:
1. Robotic Inspection
Robotic arms equipped with cameras and sensors are used to inspect vehicle bodies for defects. These robots can identify issues like paint imperfections or misalignments with high accuracy.
2. Machine Vision Systems
Machine vision systems are used to inspect individual components, such as engine parts or electronic components. These systems can detect tiny defects that might go unnoticed during manual inspections.
3. Autonomous Testing Vehicles
Automakers are developing autonomous vehicles specifically designed for testing purposes. These vehicles can assess vehicle performance, safety features, and driving characteristics under various conditions.
In conclusion, when it comes to ensuring top-notch product quality while managing high-volume production, Automated Quality Control (QC) emerges as the superior choice. While manual QC has its merits for smaller batches and cost-efficiency, it can struggle to keep pace with the demands of large-scale operations. On the other hand, Automated QC brings a winning combination of consistency, speed, and reliability to the table. Although it requires an initial investment and technical know-how, its long-term benefits far outweigh the costs. With the right expertise and implementation, automation experts can significantly enhance productivity, capacity, and overall product quality. It's clear that embracing automated QC can lead to improved efficiency and customer satisfaction, ensuring the sustained success of any business in today's competitive landscape.
Contact Us for Free Consultation
Ready to take your business to the next level with automated machines and systems? Contact us today at +60 19 268 9812 (Mr. Rajaa) for a free consultation. Our experts will help you explore the best solutions tailored to your specific needs, ensuring a seamless integration of cutting-edge technologies into your production processes.
© 2024 T-Robot. All Rights Reserved.