How Can Automated Water Bottle Production Quench Your Business's Thirst for Efficiency?
11/1/20236 min read
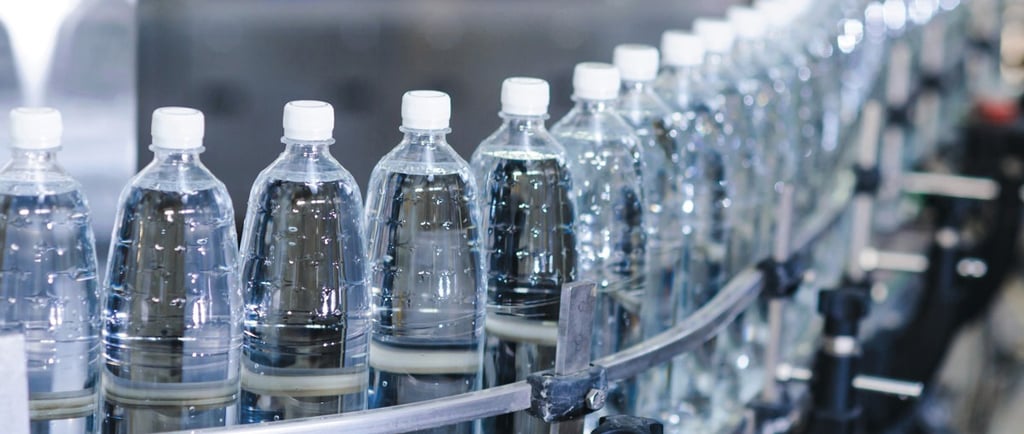
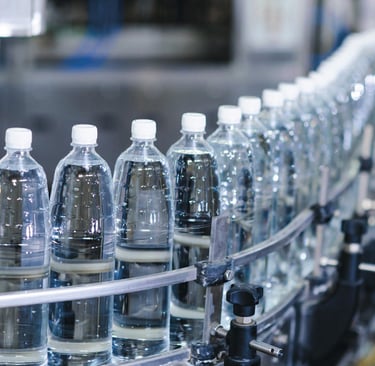
In the fast-paced world of manufacturing and business, efficiency and productivity are paramount. If you're in the water bottle manufacturing industry, you're well aware of the competitive nature of this market. To stay ahead of the curve and meet the increasing demand for bottled water, many businesses are turning to automated production systems. In this comprehensive guide, we'll explore the numerous advantages of automated water bottle production and how it can benefit your business
Introduction
Water is a fundamental element of life, and its consumption is on the rise globally. As a result, the bottled water industry has grown exponentially, creating fierce competition among manufacturers. To thrive in this demanding market, manufacturers must adapt to the changing landscape and meet the increasing consumer demand for convenience, quality, and affordability.
Automated water bottle production has emerged as a key solution for businesses seeking to stay competitive and enhance their operational efficiency. This article will delve into the numerous benefits of automated production systems, demonstrating why they are a smart choice for business owners and manufacturers in the water bottle industry.
The Rise of Automated Water Bottle Production
In the past, water bottle production was a labor-intensive process. However, with advancements in technology, automated systems have become more accessible and cost-effective. Automated water bottle production refers to the use of machinery and technology to handle various production tasks, from preform molding to filling, capping, labeling, and packaging.
Here are some of the key benefits of adopting automated water bottle production systems:
1. Increased Efficiency
One of the most significant advantages of automated production is the substantial increase in efficiency. Automation minimizes the need for manual labor and reduces the potential for errors. Machines can operate 24/7 without fatigue, leading to higher production rates and lower operational costs.
2. Improved Quality Control
Automated systems can consistently produce high-quality water bottles, ensuring uniformity in shape, size, and overall product quality. This level of precision is challenging to achieve with manual production methods, where human errors can lead to defects in the final product.
3. Cost Savings
While the initial investment in automated equipment may be significant, the long-term cost savings are substantial. Reduced labor costs, less material wastage, and increased production efficiency all contribute to a healthier bottom line.
4. Enhanced Flexibility
Automated production systems can be easily adapted to accommodate changes in bottle design, size, or labeling requirements. This flexibility allows manufacturers to respond quickly to market trends and customer demands.
5. Energy Efficiency
Modern automated production systems are designed to be energy-efficient. They are equipped with features such as variable speed drives and advanced control systems that optimize energy consumption, reducing operating costs and environmental impact.
6. Consistent Productivity
With automated production, there's no need to worry about employee downtime, breaks, or shift changes. Machines work consistently, ensuring a steady production rate that meets market demands.
7. Enhanced Safety
Automation reduces the risk of workplace accidents and injuries associated with manual labor. It also ensures a more controlled and safe production environment.
8. Reduced Human Error
Human errors can be costly in terms of time, materials, and product quality. Automated systems minimize these errors, leading to a higher standard of production quality.
Components of an Automated Water Bottle Production System
Before diving further into the benefits of automated water bottle production, let's take a closer look at the various components that make up a typical automated production system:
1. Preform Injection Molding: This stage involves injecting molten plastic into molds to create preforms, which will later be blown into bottles.
2. Bottle Blow Molding: Preforms are heated and stretched to create the final bottle shape.
3. Filling and Capping: The bottles are filled with water and sealed with caps. Automated systems can handle a wide range of bottle sizes and cap types.
4. Labeling and Packaging: Labels are applied to the bottles, and they are then packed into cases or cartons, ready for distribution.
5. Quality Control: Automated systems often incorporate quality control measures, such as vision inspection systems, to ensure product integrity.
Now that we have a clear understanding of what automated water bottle production entails, let's explore the specific benefits of adopting this approach for your business.
The Benefits of Automated Water Bottle Production
1. Enhanced Production Speed
Automated production systems are designed for high-speed operation. They can consistently produce a large number of bottles per minute, significantly increasing your production capacity. This is especially important in a market where consumer demand can vary and where you need to meet peak demands quickly.
2. Improved Consistency and Quality
Consistency is a vital factor in any manufacturing process, but it's particularly critical in the production of water bottles. Automated systems ensure that each bottle meets the same high-quality standards, with minimal variations in size, shape, and labeling. This leads to improved customer satisfaction and brand reputation.
3. Reduced Labor Costs
Labor costs are a substantial part of the overall expenses in any manufacturing operation. Automated systems significantly reduce the need for manual labor, resulting in reduced wage bills, benefits, and associated HR costs. This not only lowers operational expenses but also minimizes the reliance on skilled labor, making it easier to manage your workforce.
4. Efficient Material Usage
Automated systems are designed to optimize material usage, reducing waste. This can be achieved by precise control of preform injection and blow molding processes. Less material wastage not only conserves resources but also lowers material procurement costs.
5. Faster Changeovers
In a dynamic market, the ability to switch production runs quickly and efficiently is crucial. Automated systems can be reconfigured and reprogrammed to accommodate different bottle sizes, shapes, and label designs, reducing downtime between production runs. This flexibility allows your business to adapt to changing consumer preferences and market trends with ease.
6. Lower Maintenance Costs
Automated machinery typically requires less maintenance than manual labor. While you'll still need routine maintenance and periodic checks, the need for repairs due to human error or wear and tear is significantly reduced. This translates to lower maintenance costs and increased machine uptime.
7. Improved Traceability
In the event of a product recall or quality issue, automated systems make it easier to trace and identify affected products. Each bottle can be tracked through the entire production process, from the molding of the preform to packaging.
8. Energy Efficiency
Modern automated systems are designed with energy efficiency in mind. They incorporate features like variable speed drives and advanced control systems that optimize energy consumption. This not only reduces operational costs but also aligns with sustainable and eco-friendly manufacturing practices.
9. Real-time Monitoring and Control
Automated systems often come equipped with real-time monitoring and control capabilities. This allows manufacturers to track the production process, identify potential issues, and make immediate adjustments, ensuring consistent product quality and efficient production.
10. Scalability
As your business grows, automated systems can be easily scaled to accommodate increased production demands. This scalability ensures that your manufacturing capabilities keep pace with market requirements, preventing the need for significant capital investments in new equipment.
Case Study: The Success of XYZ Bottling Company
To illustrate the real-world benefits of automated water bottle production, let's take a look at a case study featuring the XYZ Bottling Company.
XYZ Bottling Company, a medium-sized water bottle manufacturer, was facing challenges in meeting the increasing demand for its bottled water products. Their manual production processes were unable to keep up with the growing consumer preference for bottled water, which led to production delays, inconsistent product quality, and a spike in labor costs.
The company decided to invest in an automated water bottle production system, which included preform injection molding, bottle blow molding, filling, capping, labeling, and packaging. Here are the results:
1. Production Capacity: The automated system allowed XYZ Bottling Company to double its production capacity. They could now produce over 60,000 bottles per hour, meeting market demand more effectively.
2. Consistent Quality: Automated quality control measures ensured that each bottle met stringent quality standards. This significantly reduced product recalls and customer complaints.
3. Labor Cost Reduction: The company was able to reduce its labor force by 40%, resulting in substantial cost savings.
4. Reduced Material Wastage: Automated systems optimized material usage, lowering material procurement costs by 20%.
5. Quick Changeovers: XYZ Bottling Company could easily switch between different bottle sizes and label designs, which was vital in responding to market trends swiftly.
6. Lower Maintenance Costs: Routine maintenance costs were cut by 30%, as the machines required fewer repairs and had a longer operational lifespan.
7. Energy Efficiency: The company experienced a 15% reduction in energy consumption, resulting in both cost savings and a more environmentally friendly manufacturing process.
XYZ Bottling Company's investment in automated water bottle production not only helped them remain competitive in the market but also led to improved profitability and customer satisfaction.
In conclusion, automated water bottle production offers a multitude of benefits to business owners and manufacturers in the industry. The shift to automation can enhance production speed, product quality, and cost-efficiency. Additionally, it allows for greater flexibility in responding to market demands and changing consumer preferences.
The case study of XYZ Bottling Company demonstrates how an investment in automation can yield significant returns, including increased production capacity, reduced labor costs, and enhanced product quality. In today's fast-paced business world, automation is not just a luxury but a necessity for those looking to thrive in the water bottle manufacturing industry.
If you're interested in exploring the possibilities of automated water bottle production for your business or if you have any questions, please feel free to contact us at +60 19 268 9812 (Mr. Rajaa) for a free consultation. Our team of experts is here to help you make an informed decision and provide guidance on how automation can benefit your specific manufacturing needs.
Investing in automated water bottle production can be a game-changer for your business, offering a competitive edge that can propel you to the forefront of the industry. Embrace the future of manufacturing with automation and enjoy the numerous advantages it brings to your operations.
© 2024 T-Robot. All Rights Reserved.